In an earlier blog we discussed the importance of delivered particle size for orally inhaled products (OIPs) and in a recent FAQ, we explained why cascade impaction is the sizing technique of choice. In this blog post, we’re going to take a closer look at compendial specifications for aerodynamic particle size distribution (APSD) measurement for different OIPs and how they shape the associated cascade impactors test set-ups.
Test conditions: how do they vary and why?
Compendial methods for APSD measurement reflect the way in which different devices operate and are used. However, it’s worth remembering that these methods were developed principally for quality control rather than for clinically relevant information gathering; usability, repeatability and reproducibility are the defining focus. A primary difference between methods is test flow rate but there are also additional points to be aware of when it comes to establishing a test set-up for different devices:
Metered Dose Inhalers (MDIs) are tested at a flow rate of 28.3 or 30 L/min. With MDIs, drug delivery is propellant-driven which means that the inhalation profile of the patient has minimal effect on the delivered dose. The 28.3 L/min is a historical convenience relating to the use of the ACI (see below); the NGI was calibrated at 30 L/min for ease. When testing MDIs with spacers/VHCs, time delays are specified to assess the impact of uncoordinated use since patients may inhale immediately after actuation, or some seconds later.
Nebulisers are tested at a flow rate of 15 L/min to reflect the relatively low air flows associated with tidal breathing, as applied during product use; the application of a tidal breathing pattern is complicated by the need for constant air flow through the cascade impactor. Impactor cooling (to 5 °C) is recommended to minimise the risk of solvent loss and droplet size change, notably for solution formulations, since this can skew APSD measurements.
Dry Powder Inhalers (DPIs) are tested at the flow rate required to generate a 4 kPa pressure drop across the device, up to a maximum value of 100 L/min. With a DPI, aerosolisation and delivery of the dose is typically driven solely by the inhalation manoeuvre of the patient; characterisation is therefore particularly sensitive to test flow rate. 4 kPa is representative of the average pressure drop drawn by an adult male following the instruction to breathe quickly and forcefully. But there is an additional requirement to test DPIs under sonic flow conditions to ensure flow stability. Test time is also specified, on the basis of total inhaled volume (2 or 4 L depending on the specific pharmacopeial/regulatory guidance being followed, see below).
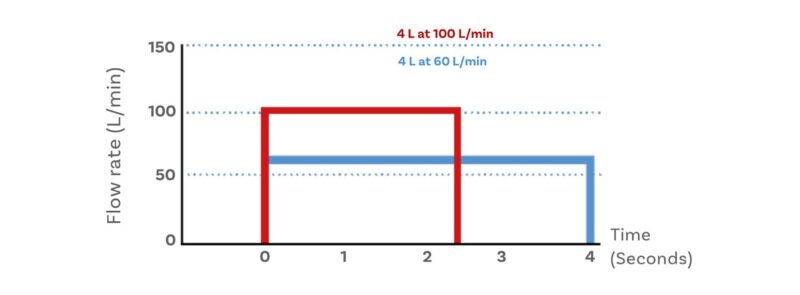
The relationship between flow rate and test time for DPI
Focusing on the impactor: which to choose and why?
The two most widely used cascade impactors are the Andersen Cascade Impactor (ACI) and the Next Generation Impactor (NGI).
The ACI (left) and NGI (right)
The ACI cascade impactors were originally designed for air sampling and analysis, and to operate at an air flow rate of 1 SCFM (standard cubic foot per minute), 28.3 L/min. Decades ago, we began manufacturing the ACI to tighter specifications and higher standards than this original application demanded and today it is available in titanium, stainless steel, and aluminium.
Pros include: Good corrosion resistance (material of construction can be matched to formulation requirements), an easy-to-handle stacked design (damaged stages are simply removed and replaced), and eight stages with cut-off diameters in the sub-10 µm range.
The NGI cascade impactors, in contrast, were designed specifically for pharmaceutical use by an industry-led consortium convened in the late 1990s.
Pros include: A planar layout that eases automation and allows for relatively fast manual measurement (collection cups are all inserted/removed together with no requirement for full impactor dismantling, and no potential for stage order errors), calibrated operation across the flow rate range 15 – 100 L/min, lower interstage losses, good stage efficiency, and seven stages with cut-off diameters in the sub-10 µm range at all flow rates; five in the 0.5 to 6 µm range of most interest for inhaled drug delivery.
These benefits address known limitations of the ACI, notably the lack of ‘pharmaceutical quality’ archival calibration data and the need for conversion kits to operate above 28.3 L/min (60 and 90 L/min kits are available). But, of course, the NGI also has limitations. High jet velocities make it important to consider the need for collection surface coating and careful handling is required to avoid corrosion, notably when testing at low temperature and high humidity; the NGI+ has a stainless-steel seal body and therefore offers superior performance in this regard.
The MSLI (left) and GTI (right)
For completion we also need to mention two other instruments: the Multi-Stage Liquid Impinger (MSLI) and the Glass Twin Impinger (GTI). These traditional systems lack the resolution of the ACI and NGI, having just 4 and 2 stages respectively, but do have their attractions. The MSLI has virtually no interstage losses and moist collection surfaces that eliminate particle bounce and re-entrainment; the GTI has similarly low interstage losses and is extremely simple to use and maintain.
So, which to choose?
A first point to note is that the MSLI and GTI are only retained in the Ph. Eur., not the USP. Furthermore, the GTI is only suitable for testing at a flow rate of 60 L/min; its low resolution limits application to relatively coarse QC.
The ACI and NGI are included in all pharmacopoeia specifications relating to APSD measurement for OINDPs and here choice becomes more nuanced. For those working on generics the instrument used to develop the reference product determines choice; similarly, if a lab uses predominantly legacy methods. In either of these cases the ACI is the more likely candidate.
Otherwise, key factors to consider include corrosion resistance, productivity and test flow rate. Choice of material of construction may make the ACI the preference for certain formulations, though less so now the NGI+ is available. For nebulisers, calibrated performance at 15 L/min is an additional plus for the NGI.
Key ancillaries: which are required and why?
The following ancillaries are essential across all cascade impactor set-ups:
- A vacuum pump to draw air through the set-up. Lower capacity units are fine for the flow rates associated with testing MDIs and nebulisers, but higher capacity units are needed for dry powder inhalers (DPIs), notably with the NGI because of the higher pressure drop associated with its finer cut-off diameter resolution.
- A flow sensor to ensure that air flow rate is known and constant as required for defined separation performance and by extension reliable APSD data.
- An induction port to ‘mimic’ the throat, typically the standard USP/Ph.Eur. induction port, though more realistic geometries are available for more clinically relevant measurement.
- A mouthpiece adapter to provide an airtight seal between device and induction port.
Additional ancillaries relate to the test conditions for specific devices and include:
- A flow controller for stop/start air flow control for testing Breath Actuated MDIs and conventional MDIs with spacers/valved holding chambers (VHCs), to simulate the impact of uncoordinated use.
- A critical flow controller for testing DPIs under sonic flow conditions, a condition achieved by ensuring that the pressure downstream of the flow control valve is half or less than that of the upstream pressure.
- A preseparator to capture powder boluses and larger, non-inhalable particles prior to entry into the cascade impactor.
An NGI test set-up for DPIs with mouthpiece adapter, USP/Ph.Eur induction port, preseparator, NGI, critical flow controller and vacuum pump (with additional flow sensor for determining test conditions)
Looking ahead: how are core methods evolving and why?
If we look at the compendial test set-ups from the perspective of predicting in vivo behaviour, rather than simplicity then there is scope for improvement. For example, using a breathing simulator makes it possible to apply a more patient-representative breathing profile across the device during testing; more clinically representative induction geometries such as the Alberta Idealised Throat can give a more realistic assessment of deposition behaviour.
A key motivation for such refinements is to maximise the informational output from in vitro testing (increasingly in combination with in silico methods) to reduce reliance on more time-consuming and expensive in vivo methods – a significant prize. We’ll be discussing this topic in future blogs but if your focus is getting your basic test set-up together then our dedicated web pages are a great place to start.
Impactor, impinger what’s the difference?
An impactor has dry collection surfaces, though they may be coated with a sticky substrate to reduce particle bounce, while in an impinger particles are collected in liquid reservoirs, typically a compatible solvent.